
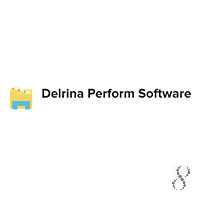
Adaptation of the design may render these systems more suited for processing large volumes, but this makes it essential to characterise the hydrodynamics of the redesigned system. Many of these microfluidic separation principles may show potential, but they need significant redesign to enable upscaling to larger volumes. Therefore, alternative separation techniques have been proposed that make use of microfluidic separation principles 4, 5, 6, 7. An effective technique to separate large volumes of these particle suspensions is microfiltration, but even this technique suffers from drawbacks like concentration polarization, cake layer formation, pore blocking and internal pore fouling 1, 2, 3.

Separating neutrally buoyant suspensions of micron-sized particles (1–10 µm) is not a trivial operation.

These findings give a new perspective on the separation principle, which makes the technique more flexible and easier to translate to industrial scale. Therefore, the geometric design criteria of DLD devices is in fact just one method to control the local hydrodynamics, which may also be influenced by other means. The size of the flow lanes strongly correlates with the local flow velocity (V y and V x), which depends on the hydrodynamics.

Flow lanes were visualized and the local flow velocities were measured using µPIV and compared with 2D fluid dynamics simulations. We here investigated why these simplified DLD systems are able to displace particles, by experimentally investigating the hydrodynamics in the device. In previous research, separation was observed in simplified DLD systems that did not meet the established DLD geometric design criteria, by adjusting the outflow conditions. The width of these flow lanes is crucial for separation of particles and determines whether particles with certain size are displaced or not. Deterministic lateral displacement (DLD) systems structure suspension flow in so called flow lanes.
